From sewage sludge to green gas and green cement
A lot is happening in water board country. And who knows, maybe the future will soon look very different if the Alkmaar-based company SCW will live up to expectations. Namely a lot greener and more circular.
SCW (Super Critical Water), located in the Alkmaar Boekelermeer, will this summer start producing green circular gas on an industrial scale from raw glycerol, among other things. This residual product from the biodiesel industry will be supercritically gasified under high pressure and temperature. This the world's first supercritical gasification plant! After glycerol, the intention is to gasify plastic and sewage sludge. For plastic, an extensive research program is currently underway to make circular gas from it that can be used again as a raw material for new plastic materials. In addition, the water boards affiliated with HVC are planning to start a similar program for sewage sludge including sludge from Hoogheemraadschap Hollands Noorderkwartier.
From centuries to seconds
In addition to this gasification technology, SCW has developed a second revolutionary technology to bind CO2 contained in the gas produced (=syngas) directly to ground rocks (minerals) that are abundant worldwide. This natural process, which normally takes centuries, SCW has been able to reduce to seconds. They call this processCO2 CLEAN UP. During this process, powders are created to which the CO2 is bound, and these powders serve as the basis for useful products. A good example is the direct application of one of these powders to make cement.
Green cement
That powder can be used as the main ingredient in this new cement. In fact, you then speak of "green cement" that can be used to make CO2 negative concrete: concrete in which you have CO2 permanently stored. The conventional way of making cement is extremely energy intensive and responsible for 5-9% of global CO2 emissions! SCW'sCO2 CLEAN UP process thus permanently sequesters CO2 in useful products and thus prevents the production of products that release a lot of CO2. Consider the example of cement and concrete. As a result, the entire process is CO2 negative, effectively reducing the CO2 concentration in the air, hence the nameCO2 CLEAN UP.
Circular business operations
The water boards would like to be the first to apply this cement. In this way, the water boards can not only contribute to the reduction of CO2 in the atmosphere, but also take the next step toward circular business operations.
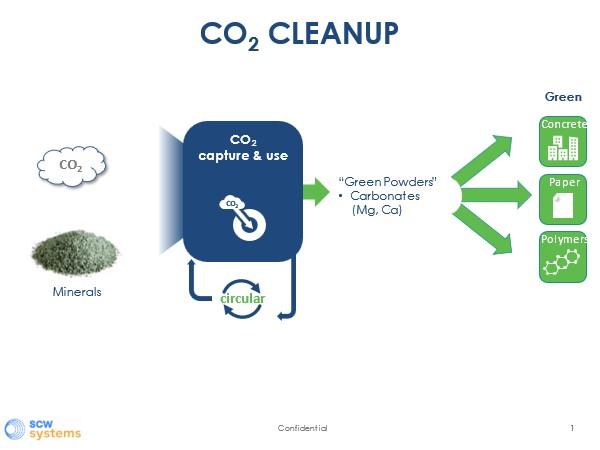
Recognition as green
Water boards also produce a lot of CO2 in biogas and would also be able to achieve large-scale negative emissions with this technology and are pulling together with SCW. But two things are important. CO2 from biogas and syngas must be recognized as green, only by capturing green CO2 extracted from the atmosphere can you realize negative emissions. In addition, SCW's technology must be recognized as an official carbon recovery and storage technology as well as the circular application technology if made into green cement. The water boards have started discussions with SCW about this with the Rijksoverheid.
Clean Up Factory
Meanwhile, work continues at Boekelermeer. SCW plans to have a CO2 mineralization plant operational in the first half of 2023 that can permanently store 15 Ktonnes of CO2 on an annual basis. This will be located on the North Holland Canal. If the expectations come true, in 2023 HHNK can start applying the first green cement products with CO2 recovered from its own biogas, directly from the atmosphere, and eventually even from its own sewage sludge.
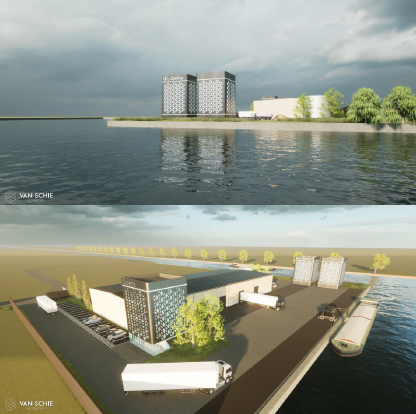